
Typical high-speed CAN devices include antilock brake systems, engine control modules, and emissions systems.
TENSION SOFTWARE DATA CREATOR ISO
Other names for high-speed CAN include CAN C and ISO 11898-2. High-speed CAN networks are implemented with two wires and allow communication at transfer rates up to 1 Mbit/s. High-speed CAN is by far the most common physical layer. The most common and widely used physical layers are described below: These physical layers classify certain aspects of the CAN network, such as electrical levels, signaling schemes, cable impedance, maximum baud rates, and more. CANopen also is used in nonindustrial applications such as laboratory equipment, sports cameras, telescopes, automatic doors, and even coffee machines.ĬAN has several different physical layers you can use. Lifts and escalators use embedded CAN networks, and hospitals use the CANopen protocol to link lift devices, such as panels, controllers, doors, and light barriers, to each other and control them. Hospitals control operating room components such as lights, tables, cameras, X-ray machines, and patient beds with CAN-based systems. In fact, some hospitals use CAN to manage complete operating rooms. Medical equipment manufacturers use CAN as an embedded network in medical devices. In addition, you can find CAN buses in many aerospace applications, ranging from in-flight data analysis to aircraft engine control systems such as fuel systems, pumps, and linear actuators. CAN also has applications in aircraft with flight-state sensors, navigation systems, and research PCs in the cockpit. You can find examples of CAN devices linking the door units, brake controllers, passenger counting units, and more on different levels of the multiple networks within these vehicles. Railway applications such as streetcars, trams, undergrounds, light railways, and long-distance trains incorporate CAN. However, as other industries have realized the dependability and advantages of CAN over the past 20 years, they have adopted the bus for a wide variety of applications. Global and local errors are differentiated by the controller, and if too many errors are detected, individual nodes can stop transmitting errors or disconnect itself from the network completely.ĬAN was first created for automotive use, so its most common application is in-vehicle electronic networking. Frames with errors are disregarded by all nodes, and an error frame can be transmitted to signal the error to the network.
TENSION SOFTWARE DATA CREATOR CODE
The CAN specification includes a Cyclic Redundancy Code (CRC) to perform error checking on each frame's contents. This also allows networks to meet deterministic timing constraints.
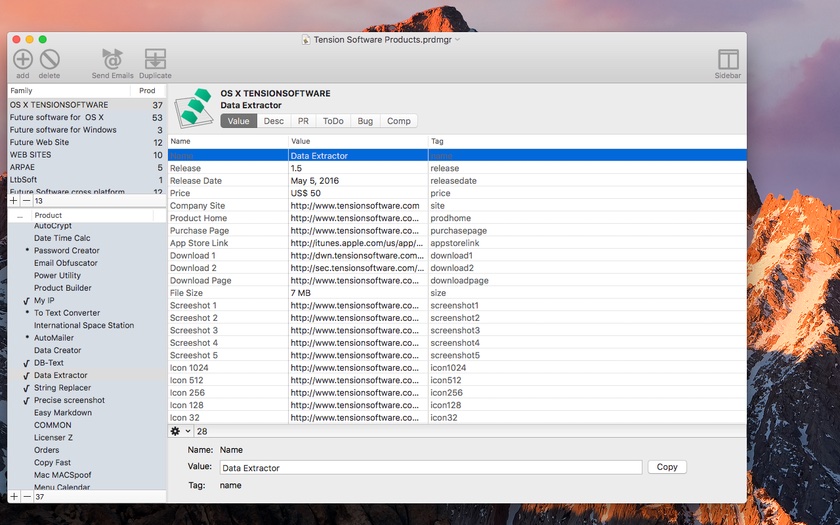
This arbitration is non-destructive and results in non-interrupted transmission of the highest priority message. PriorityĮvery message has a priority, so if two nodes try to send messages simultaneously, the one with the higher priority gets transmitted and the one with the lower priority gets postponed.

Additional non-transmitting nodes can be added without modification to the network. This structure allows modifications to CAN networks with minimal impact.
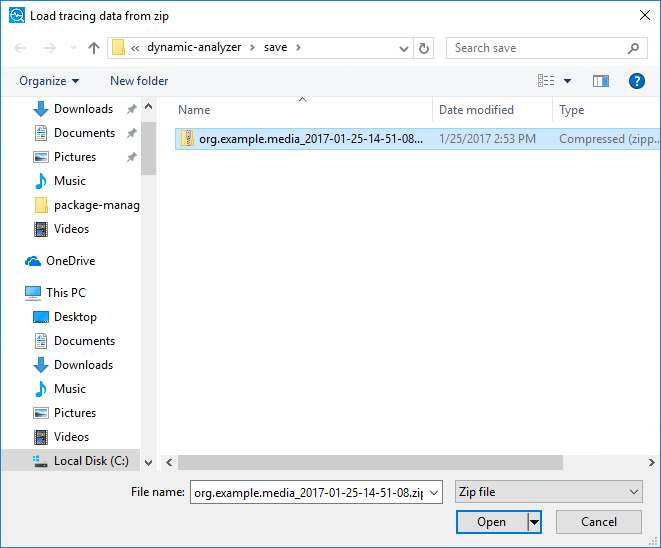
Each device can decide if a message is relevant or if it should be filtered. All devices on the network see all transmitted messages. Broadcast CommunicationĮach of the devices on the network has a CAN controller chip and is therefore intelligent. This decreases overall cost and weight in automobiles. An advantage to this is that electronic control units (ECUs) can have a single CAN interface rather than analog and digital inputs to every device in the system. CAN provides an inexpensive, durable network that helps multiple CAN devices communicate with one another.
